What is Touch-Proof Terminations and why Utilities are Switching to it?
In the evolving landscape of medium-voltage (MV) power distribution, safety, reliability, and modularity are non-negotiable. That’s why utilities and switchgear OEMs across the globe are moving away from traditional open-term systems toward touch-proof terminations, also known as screened separable connectors.
But what exactly does “touch-proof” mean—and why has it become the industry standard?
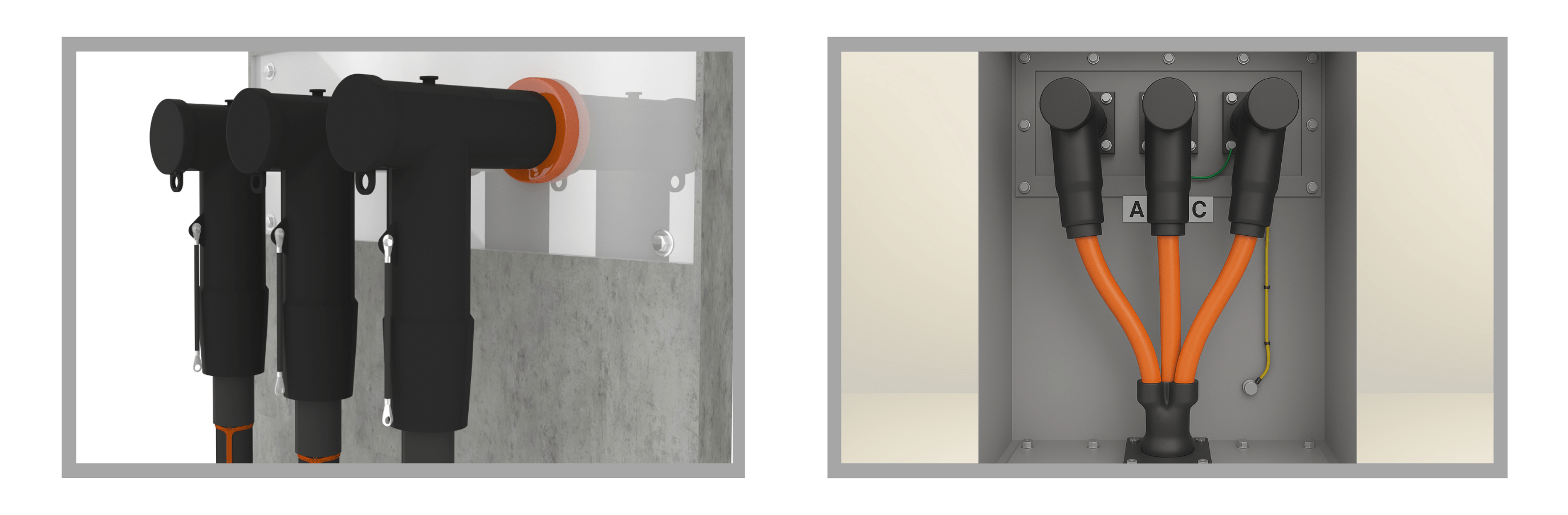
What Is Touch-Proof Termination?
A touch-proof termination refers to a fully enclosed, screened, and insulated connection system that prevents accidental contact with live conductive parts. These terminations are most commonly molded from high-performance EPDM or silicone rubber and feature an externally conductive screen that’s earthed—ensuring the surface remains at ground potential even under full operating voltage.
In simple terms: even when energized, the outer body of a touch-proof connector is safe to touch, eliminating the risk of electric shock.
Key Features of Touch-Proof Terminations
- Fully insulated and screened: Ensures complete operator safety during energization.
- Compact, elbow-shaped design: Ideal for confined switchgear and RMU chambers.
- Separable and modular: Enables easy installation, testing, and replacement.
- Submersible construction: Suitable for outdoor, wet, or underground environments.
- Compatible with EN 50181 bushings (Type C): Supports 630A, 800A, and 1250A systems.
The Problem with Conventional Terminations
- Traditional heat shrink or cold shrink terminations, while reliable, are: Exposed to air, water, and mechanical damage.
- Non-touch safe, requiring clearances and additional shielding.
- Harder to maintain or replace without full shutdowns.
Why Utilities Are Switching
- Safety First
Touch-proof terminations eliminate exposure to live parts, allowing technicians to safely work around energized equipment—critical for grid uptime and worker protection. - Space Optimization
Their compact design reduces the footprint required inside GIS panels or RMUs, enabling more compact and modular substations. - Interchangeability
Standardized dimensions (EN 50181) make touch-proof terminations vendor-agnostic— a major advantage in procurement flexibility. - Reduced Downtime
Since the terminations are separable, they allow hot-swapping of connectors, surge arresters, or T-junctions without dismantling the entire system. - Ease of Testing
Test points integrated into the elbow body allow voltage presence detection, diagnostics, and partial discharge monitoring—without disconnection.
Use Cases and Growth
Today, touch-proof terminations are becoming the preferred standard in:
- GIS and RMU connections (up to 36kV)
- Solar and wind power evacuation
- Containerized substations
- Compact metro & airport substations
- Oil & gas installations with safety-critical ratings